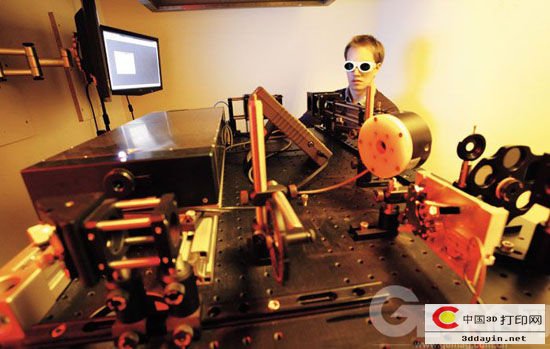
Content reading: Will the future global manufacturing center be located in Chongqing, Bangkok or Bangalore? Not right. It may exist in everyone's home, 3D printing technology comes
You may think that 3D printing is only in sci-fi movies. Even if you just hear something about it, you may ask, "This is cool, but what can you do?" But in the eyes of geek entrepreneurs like Li Guohao, the technology is not only cool, but also Very profitable. In Li's design work room, the nozzle of a 3D printer is constantly "silked" and then superimposed on a plastic plate. Less than two hours, an anime character can be formed. Each market price exceeds 100 yuan, and monthly sales are also hundreds.
Today, Shenzhen, Hangzhou and other places, there are quite a few similar entrepreneurs. All their sustenance is based on a 3D printer worth only a few thousand dollars. The doll model costs only a little over a dozen dollars. In the past, traditional toy factories developed similar dolls that only cost a few thousand dollars.
What is commendable is that this technology can be used by fools - modify the printed shape and color on the blueprint shown on the computer screen, and then press the print button. The operation process is as follows: Each layer of the printing process is divided into two steps. First, a layer of special glue is sprayed on the area to be formed. The glue droplets are extremely small and difficult to spread, and then evenly spray a layer of powder. The powder will rapidly cure the glue when it encounters the glue. The area without glue remains loose. In this alternating layer of glue, the solid model will be printed and printed. Once the loose powder is removed, the model can be "planned" and the remaining powder can be recycled. The process only needs to determine the required plastic, resin, metal and other materials, the material cost is only one-tenth that of traditional manufacturing, and the error can be easily controlled within 0.1 mm. It does not require a production line and can also produce grotesque parts that cannot be produced by conventional methods.
The benefits are not limited to this. Taking Hummer, an Israeli company that uses the 3D printing system provider Objet 3D printer, as an example, the production time of its sports shoe model can be reduced by three quarters, from four days to one day. Not only can you eliminate the hassle of remote communication, you can also reduce design errors. Luxury car makers Jaguar and Land Rover have said that more than one-third of the parts made of epoxy-based composite materials are produced by Objet's 3D printers.
This is only the beginning. Terry Wohlers, president of Wohlers Associates, has worked in the 3D printing industry for 25 years. Wallers estimated that sales of 3D printing products and services in 2011 had reached US$1.7 billion, while parts and components manufacturing operations accounted for nearly one-quarter, which was twice as much as in 2007. By 2019, the industry's revenue will reach 6.9 billion U.S. dollars, of which parts and components production is expected to account for 80%. At present, the yield of products printed directly by 3D printers has reached 20%, and by 2020 this figure will increase to 50%.
New business models will also emerge. In the United States, Shapeways, a 3D printing services company, has 150,000 members and more than 6,000 businesses—users can upload and print their own 3D productions through the Shapeways platform and sell them. So far, the company has printed over a million products for customers, and its printing materials include more than 30 kinds of materials such as ceramics, plastics and tempered glass.
The capital market also voted for the 3D printing business. Shapeways has received tens of millions of dollars in venture capital. At the beginning of August, after the domestic aluminum foil processing company Yinbang shares (20.180, -1.41, -6.53%) (300337) announced its entry into 3D printing, its share price soared by 20%, and the investment institutions quickly increased their ratings to increase their holdings.
Optimists are convinced of the following conclusions: 3D printing will subvert the manufacturing industry from the source, and machines will replace every key link such as molds, components, semi-finished products and finished products. This is a complete subversion of traditional manufacturing - labor, equipment investment, worker skills, production line management, etc. will become irrelevant.
3D printing was derived from computer-aided design in the late 1970s. The earliest production of a model, engineers often need to use computer simulation, supplemented by artificial steel, gypsum, clay, wood and other materials to make molds. It is time-consuming and laborious. It takes thousands of dollars and months for just one of the simplest plastic cases.
The equipment and consumables for early 3D printing were very expensive. In the 1990s, a 3D printer was up to several million dollars, and it was used only for upstream links such as mold development and prototype design, rather than mass production. In early 2000 this price had dropped to between one and twenty thousand dollars. Two years ago, open source 3D printer maker Makerbot lowered its cost to less than US$2,000, while on Taobao, you could purchase a similar device for less than 4,000 yuan.
The low price has promoted the rapid popularization of 3D printers. These inexpensive 3D printers cannot completely replace the traditional manufacturing processes such as injection molding, but it is more than sufficient to print some product prototypes and simple toys. But just as no one can predict the impact of the 1450 Gutenberg print, the 1750 steam engine, and the appearance of the 1950 transistor, the lasting impact of 3D printers remains to be assessed. There is no doubt that it will expand the limits of industrial imagination. In the future, 3D printers will fight alongside traditional manufacturing equipment such as milling machines, castings, injection molding, and even replace them. With the increase of printing yield, the demand for employment in the future will also be greatly reduced.
This is not worrying people. Shapeways, a 3D printing company, has been able to use Nylon 12 direct printing to create seamless splicing swimsuits. This is only the beginning, and any kind of clothing in the future will be made by digital technology without the need for manual or sewing machines.
Will this be a Chinese-made nightmare? "The greatest advantage of 3D printing is to increase the number of machines and increase the production capacity. Moreover, machines are a one-time investment and only need to consider electricity charges. Manpower processing must be continuously invested." Yu Tao, a senior mechanical engineer, said to "Global Entrepreneurs." A conventional injection molding line requires at least 5 to 6 workers to operate, and a technician can manage dozens of fully automated production facilities. The greater disruption lies in the flexible supply chain. In the traditional manufacturing model, when the customer puts forward the production demand, it must determine the quantity of each batch according to market expectations and carry out batch production. Once the plant is put into operation, even if the supply exceeds demand or supply exceeds demand, the production line will be difficult to stop. For 3D printing, you can print the experimental product first, and then make a decision based on the market feedback effect.
Future 3D printing will reduce the status of some traditional manufacturing centers. For example, the advantage of the Shenzhen mobile phone industry lies in an efficient supply chain system. Both upstream and downstream can clearly grasp the trend of the market, and once the product is sold or sold hot, the production strategy can be adjusted. But in the era of 3D manufacturing, these are not important. 3D printing can be stopped immediately at any time. Whether it is located in Shenzhen or the United States, the factory can obtain sufficient production capacity and response speed. The labor cost and technician level can be ignored.
Future 3D printers will be able to print any product on demand. Consumers do not need to purchase products that are streamlined in traditional factories, but only purchase 3D printers and product drawings. It is expected that labor-intensive products such as shoes, hats, cutlery and toys will bear the brunt.
(Editor)