In the process management of carton enterprises, standardization is one of the important tools. It is very important and necessary for carton enterprises to attach importance to and strengthen process standardization. Process standardization is an important step in the standardization of carton enterprises, and the standardized control of each process link in the carton production process is an important part of process standardization.
As one of the key links in the production of carton, corrugated board production often has problems such as disorderly production schedule, frequent quality accidents, and low efficiency, which greatly affects the efficiency and customer satisfaction of carton enterprises. In order to avoid such problems, carton enterprises can formulate uniform standards for process factors, process parameters and process documents according to the production characteristics of corrugated board production lines. Its role lies in: First, it is of great significance to improve the technical level of the process, ensure the stability of product quality, improve production efficiency, reduce labor intensity, improve the utilization rate of raw materials, and strengthen process management. Second, to make employees "documents, operation and intention", will The standardized documents in the mind are put into actual operation, standardizing and guiding operations, thus simplifying production, organizing production, directing production and guiding operations; third, operating the employees through the management method of “changing thinking with behavior†Constraining, eliminating the behavior of arbitrary operation, escorting the next process and the quality of the carton, so that the employees form the overall situation of the overall process considerations. Here, the paper will introduce the process control and standardization of corrugated board production line according to the actual situation of the author's enterprise.
Process and control points for corrugated board production lines
Figure 1 shows the process flow and control points of the corrugated board production line. The requirements of each control point are as follows.
Control Point 1: Accurately verify the original paper information on the voucher, including the width, weight, manufacturer and special requirements of the base paper.
Control point 2: Glue is strictly in accordance with the procedure of making rubber, and the adhesive index should be qualified.
Control Point 3: Ensure that the dimensions are correct.
Control point 4: The amount of glue applied, the temperature inside the drying belt, and the tension value are executed in accordance with the “Technical Standards†of the corrugated board production line established by the company.
Control point 5: Cardboard flatness, neatness, corrugated forming effect, high height, and adhesion strength are in line with the quality standard of the chopped board production line established by the company.
Control Point 6: Adjust the process specifications to be within the scope of the Process Standards.
Process standardization of corrugated board production line
1. Adhesive index
The viscosity and solid content of the adhesive for corrugated board should be adjusted according to the season. Generally, when the temperature is low and low humidity (winter), the adhesive viscosity of the single corrugated board is 17-21s (coating 4 cups, the same below), the solid content is 17%-19%; the viscosity of the adhesive for the three corrugated board is 40~ 60s, solid content is 18% to 20%. In high temperature and high humidity (summer), the adhesive viscosity of single corrugated board is 20~25s, the solid content is 19%~22%; the adhesive of three corrugated board is 55~90s, the solid content is 21%~25 %. In addition, the adhesive should be stretched (use a thumb to stick a little adhesive, and the index finger, slowly pull the two fingers until the distance between the two fingers when the adhesive breaks) is 15 ~ 20mm.
2. Base paper index
(1) The moisture content of the base paper. The moisture content of the base paper should be 6% to 8%, which is most advantageous for the bonding and corrugating effect of the corrugated board. The difference in water content between the three base papers and the left, center and right sides of each base paper shall not exceed 3%.
(2) Raw paper production time. The production dates of the three types of base paper must be similar before they can be used on the machine.
(3) The number of times the base paper is resistant to folding. The base paper should be produced in a low-temperature and low-humidity environment. In order to prevent the quality of the carton from bursting due to the low number of folding resistance, the folding speed of the base paper must be more than 50 times.
(4) Base paper strength. The strength of the base paper is determined according to the customer's pressure resistance requirements for the corrugated box used and the production process of the carton. If the compressive strength of a box type carton reaches 1500N, through analysis and calculation, if the offset printing carton is used, the base paper should be high-strength A grade, the quantitative value is 120g/m2, and the ring pressure index is greater than 7N・m/g; Or pre-printed printing carton, the base paper should be high-strength A grade, the quantitative is 110g/m2, and the ring pressure index is greater than 6N・m/g.
The choice of the strength of the base paper is complicated and must be determined after analysis, calculation and test according to the relevant technology. Once it is determined, the base paper must not be replaced for this type of box, and the base paper of the corresponding strength specified must be selected for production.
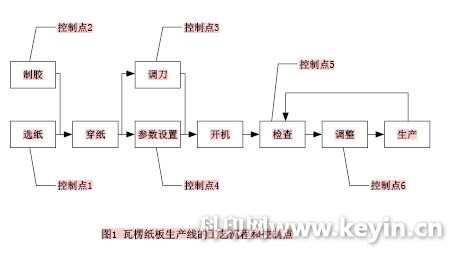
3. Original paper force adjustment
The original paper strength should be adjusted according to the longitudinal bending of the corrugated board and the use. When the corrugated board is bent in the direction of a certain longitudinal direction of the paper, the tension of the base paper should be released. The original paper core and the external tension control are different. The original paper force parameter must be reduced at the core to prevent the paper from breaking. If the original paper force is too large, it may cause quality problems such as broken paper, longitudinal bending of corrugated cardboard, and unsatisfactory corrugated forming effect. On the contrary, it may cause foaming and warping of corrugated cardboard.
4. Preheating wrap angle
The surface temperature of the preheating drum must reach above 100 °C, and the temperature of the hot platen must reach above 150 °C. The preheating wrap angle is proportional to the contact area of ​​the base paper on the preheating roll and the moisture content of the base paper. During the production process, the preheating wrap angle can be increased or decreased according to the lateral bending degree of the corrugated board. For example, when the single corrugated cardboard and the three corrugated cardboard are bent in the transverse direction, which kind of base paper is bent, the preheating wrap angle of the base paper is increased, and the preheating wrap angle of the other base paper is reduced.
5. Stack paper adjustment
Although stacking paper at the bridge helps the volatilization of the corrugated board, excessive stacking of paper can cause the corrugated board to appear on the board, bend and so on. Therefore, it is necessary to reasonably control the amount of pile paper according to the effect of the board.
10Pcs Baby Wipe,10Pcs Kleenex Wet Wipes,10Pcs Baby Aqua Wipes,10Pcs Baby Cloth Wipes
DONGYANG COMEXA SANITARY PRODUCTDS LTD.,CO , https://www.comexawetwipes.com