1. Ceramic printing ink
Ceramic printing can be printed on decal paper first, then transferred to ceramic, or printed on ceramic and glass surface, dried by oxidation or volatilization, calcined at high temperature of 450-1000 ℃, to remove the binder in the ink . The pigment is fused on the porcelain and oxidized to show color.
The ceramic decal printing ink for printing ceramic decals, the pigment includes two parts: colorant and mediation agent. The colorant mostly uses metal oxides and a few sulfides and selenides. The main components of the mediation agent are lead, quartz, Borax and boric acid. The ratio of the two varies with the color of the metal oxide. The role of the mediator is to make the metal oxide melt evenly, produce gloss, and reduce color. When ceramic printing ink is overprinted, it should be noted that similar colors can be overprinted, and different colors cannot be overprinted, otherwise chemical changes will occur at high temperatures, causing cross-colors and popping. Spot colors are also used in printing, instead of mixing the three primary colors to produce colors.
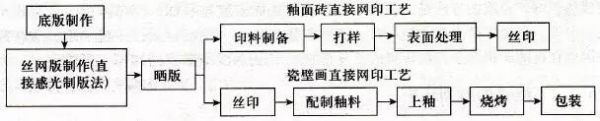
2. Glass printing ink
There are many forms of glass printing inks, mainly printed by screen printing methods. It consists of three components, ceramic pigment, glass powder and binder, to form paste color. After printing and curing, it is baked in a heating furnace at 600 ° C to vaporize the connecting material, and the pigment is consolidated on the glass by the molten glass powder, which is used to print glass bottles, cups and plates. The ceramic pigments used are titanium oxide {white}, cadmium yellow (yellow), cadmium red (red), cobalt blue (blue), chromium oxide {green}, cobalt green (green), and ferric oxide (brown). The glass powder is mainly silicon dioxide, lead oxide, boron oxide, and is often accompanied by other gold scrap oxides to reduce the softening point and improve the resistance performance. There are hydrogenated rosin esters, pine oil and other substances in the binder, which are vaporized before the glass is melted to prevent the carbonization of the ink layer. Another kind of glass printing ink melts when heated to 70-80 ° C, has a certain viscosity, can be screen printed, and solidified at normal temperature, and is used to print glass cups and beverage bottles. Epoxy type two-component inks are commonly used for screen printing small glass containers (such as cosmetic bottles, ashtrays). The commonly used one-component epoxy resin ink can reach dryness within 10-15 minutes after printing, but it needs to be baked at 180 ° C for 10 minutes to form a stronger ink film.
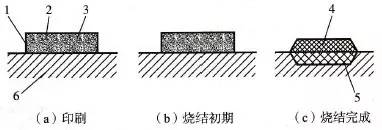
Glass printing ink
Oue dinnerware products includes knife and for set, ceramic plates set, red wine glass set and red wine goblet.
Knife And Fork Set,Ceramic Plates Set,Red Wine Glass Set,Stainless Steel Red Wine Goblet,Glass Tumbler
Shangwey Cookware Co.,Ltd of Jiangmen City , https://www.shangwey.com