PS version of the plate is used contact exposure printing, the process is as follows.
In the graphic exposure process, the film is first covered on the surface of the PS plate, and the graphic image on the film is projected onto the photosensitive layer of the PS plate through a printing plate light source. In order to obtain a clear image, the photosensitive film of the film and the PS plate needs to be tightly closed during exposure, and no gaps are allowed. Therefore, a vacuum suction frame is usually used to place the film and PS plate between the glass plate and the blanket of the vacuum frame of the platen, and then vacuum is applied to make the film and the photosensitive plate of the PS plate tightly adhered.
However, in this manner of exposure, since the surface of the PS plate is smooth, the edges of the close portion of the photosensitive layer of the film and the PS plate are easily adhered to each other, which is not conducive to the extraction of air in the middle portion, resulting in a long time for vacuumization and greatly reducing plate making. The efficiency of the operation; and sometimes after a long time, the air has not been emptied. As the domestic offset printing plate is commonly used in the positive PS version, the photosensitive resin will decompose and release a certain amount of nitrogen when exposed, as shown in Fig. 1. If it cannot be eliminated in time, it will also cause gaps between the PS and the film. As a result, the dots in the middle of the printed version of the printed document appear imaginary, resulting in blurred images.
In order to improve the quality of adhesion between the printing plate and the film and shorten the time for vacuum adhesion, people began to use the method of applying a rough surface layer on the photosensitive layer of the PS plate. Due to the presence of matte-faced particles, the surface of the photosensitive layer of the PS plate becomes rough, and a slight gap is created between the film and the photosensitive layer, so that the air in the middle portion can be easily extracted and the time for vacuuming is reduced. Therefore, the rough surface is also referred to as the gas-guiding layer.
Another effect of the rough surface layer is that when a large number of PS plates are stored in a stacked manner, the photosensitive layer of the PS plate may stick to the back surface of the upper PS plate and cannot be easily peeled off. This phenomenon is called tack. . The solution to this problem is usually to add a liner to isolate the plate, but this will create new problems. When using the PS plate, additional labor is required to remove the liner, a large amount of the liner becomes industrial waste, and some are automatic. The platesetter cannot automatically strip the paper. The rough surface can well solve the above problems.
Rough surface performance requirements
For the performance of the matte layer, in addition to the impact on the sensitivity and processing performance of the PS plate, there are the following requirements:
1. Vacuum adhesion
Compared to ordinary PS plates, the vacuum tightness of the PS plate of the frosted surface during the exposure of the text should be significantly shortened. The vacuum adhesion time is the basic index for evaluating the performance of the matte layer.
2. Developability
The matte layer should be soluble in water and alkaline developer, easily removed in the PS plate development step, and no residue after development. The plate can maintain good developing performance in the old developer, or under high temperature and high humidity conditions.
3. Storage stability
The matte layer should be able to resist the friction and pressure of the PS plate during storage and transportation without crushing and flaking, that is, having a certain degree of fastness. If the surface layer has insufficient fastness, not only does it affect the vacuum adhesion, but also the napped granules easily fall off into powder, contaminating the glass surface of the printer, and the powder tends to clog the vacuum pump during vacuuming. At the same time, it is required that no sticking phenomenon occurs on the rough surface when stored under conditions of high temperature and humidity.
Rough material
In the early rough surface applications, hot melt solid powders and other particles were applied directly to the surface of the photosensitive layer. These rough surface layers have the disadvantages of easily broken particles, easy detachment, and poor mechanical strength. Ultra-fine polyethylene particles are directly dispersed in the photosensitive adhesive and coated together with the photosensitive adhesive. The fastness and strength of the mat layer using this process are good, but the coating solution needs to be filtered when it is added to the coating tank. Polyethylene particles can easily block the filter element; since the 1980s, the use of water-soluble resin aqueous solution coating method, the main particle material of carboxyl resin and sulfonic acid-based resin, can effectively improve the rough surface layer of fastness However, such resins have strong hygroscopicity, are sticky in high-temperature, high-humidity environments, and are sticky during storage; in order to solve the sticking problem, there are also alkali-neutralizing acrylic resins, but due to the addition of alkaline substances, The photosensitive layer decomposes after storage for a long time, shortening the shelf life.
Since the 1990s until now, technologies have been developed to produce a matte layer using a dissolved or dispersed aqueous solution of an acrylic copolymer, and various properties can be well balanced. The solvent of the matte coating liquid is generally water or an aqueous organic solvent. This is mainly for safety and environmental considerations, and at the same time, the lowest cost and better results can be obtained.
Rough surface production process
The coating method of the matte layer can be sprayed and electrostatically coated, and screen printing or gravure printing can be used. Now, the rotary atomization electrostatic spraying method is used more often. The process is shown in Fig. 2. In the rotary atomization electrostatic spraying device 3, the aqueous solution of the dissolving or dispersing resin is atomized by using the centrifugal force of the cup-like spray head and the high voltage applied thereto, in the spray head and the PS plate 1 Under the action of a high electric field, atomized and electrostatically charged fine droplets fly to the surface of the photosensitive layer for electrostatic attachment, as shown in FIG. A few seconds later, the PS plate passes through the drying chamber 4 and is dried in a high-temperature, low-humidity room atmosphere or by blowing warm air.
The size and coating amount of the matte surface particles have a great influence on the performance of the PS platen matte layer. If the matte particle size is too large, or if the coating amount is too large, the contact surface between the two PS plates becomes small, the sliding property is insufficient, and the photosensitive layer is easily scratched. Larger matte particles will cause the particles to have high peaks, and the gap between the film and the photosensitive layer of the PS plate will be so large that the fine image will be difficult to reduce, and the density of the high-light part of the dots will decrease, and the image tone level will be lost. If the particle height is too small, the gap is too small, the vacuum adhesion is insufficient, and the imaging is blurred. The amount of coating is too small.
Of course, increasing the surface roughness in the PS layout will inevitably lead to an increase in the production cost of the PS version. However, from the point of view of the various benefits brought about by the rough surface layer, it is necessary to add a rough surface layer and it is also a requirement for the development of high-quality PS plates.
Source: Ke Yin Media
Measurements (m) | can be customized |
Certificate |
ISO14001, ISO18000, ISO9001 Certificate,
and GS certificate from TUV Company of Germany.
|
Color | Various, according to your requirements |
Materials |
A. Plastic parts: Imported LLDPE E. Outer cover: Soft Covering PVC
(Different material is available according to your needs)
|
Advantage |
a.Anti-UV
b.Anti-static
c.Security
d.Environmental protection e.Uneasy to lose shape |
Function |
1.Can protect children safe when they playing indoor, and let they enjoy the play freely 2.Suitable for improving Children energy and imagination 3.Helping them grow up happily, cleverly, and healthily |
Installation | Professional CAD instruction, assembly procedure and project case . |
Age Range | Children |
Apply to | Amusement park, gymnasium, Kindergarten, Preschool, etc. |
Packing | Standard export packing |
Remark |
We can design and produce as your requirements |
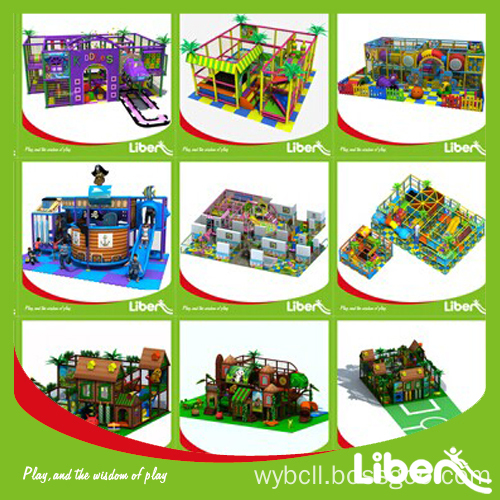
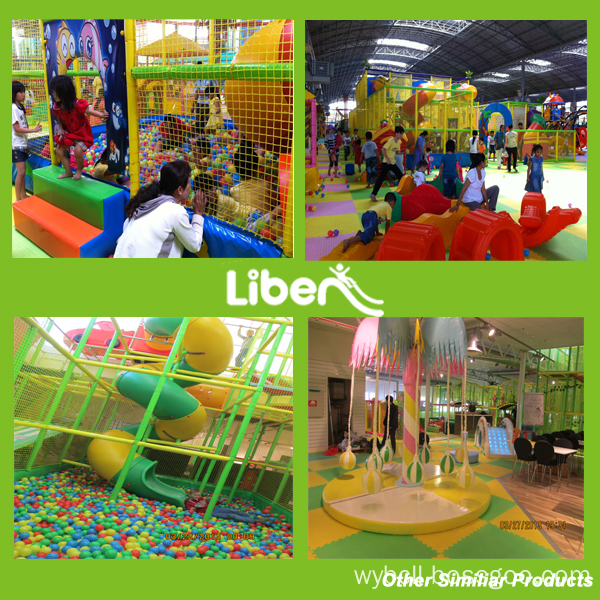
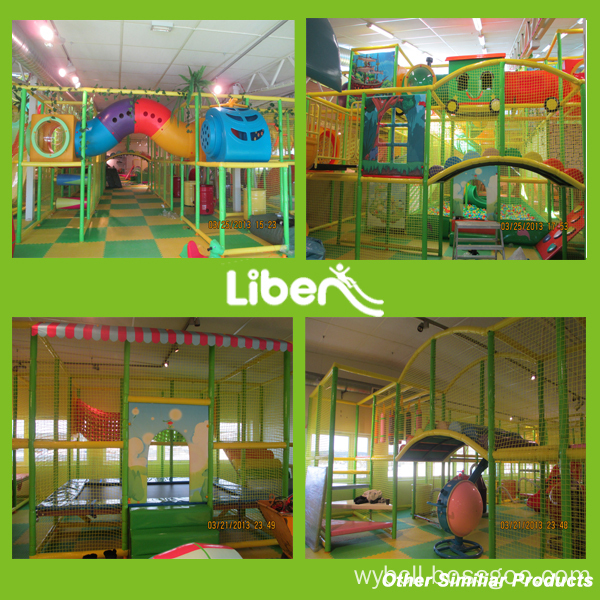
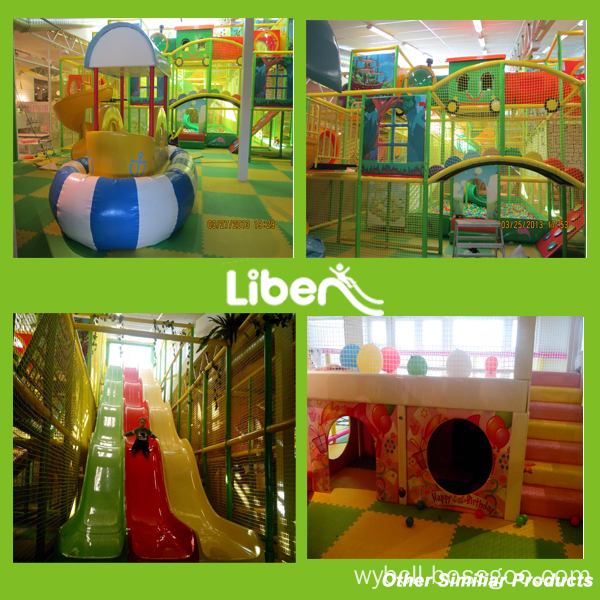
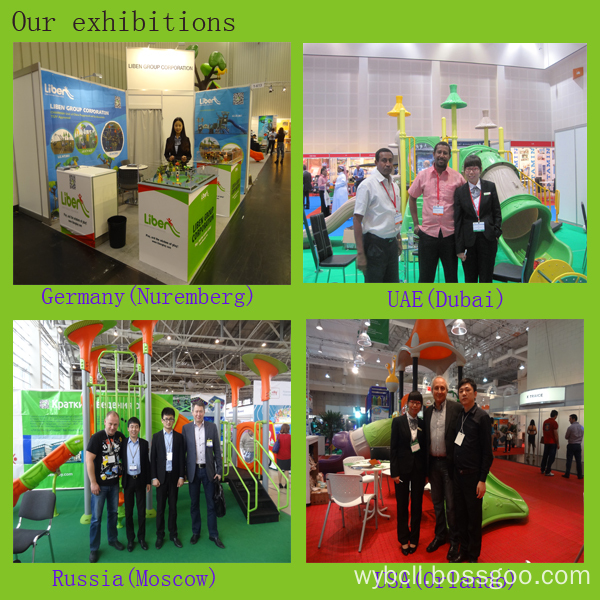
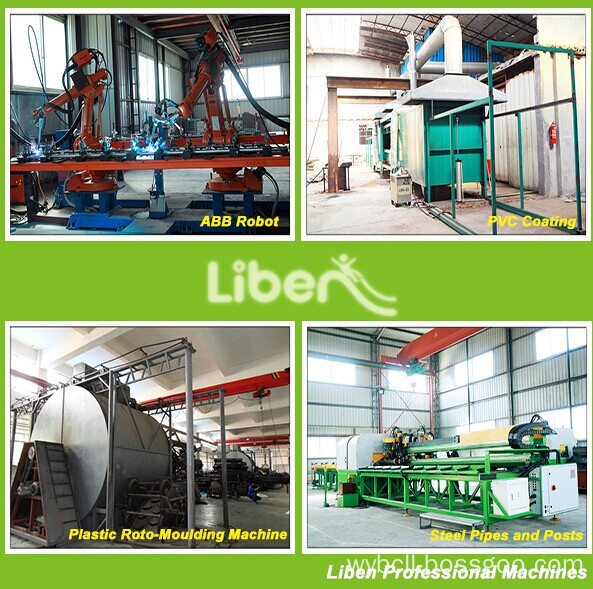
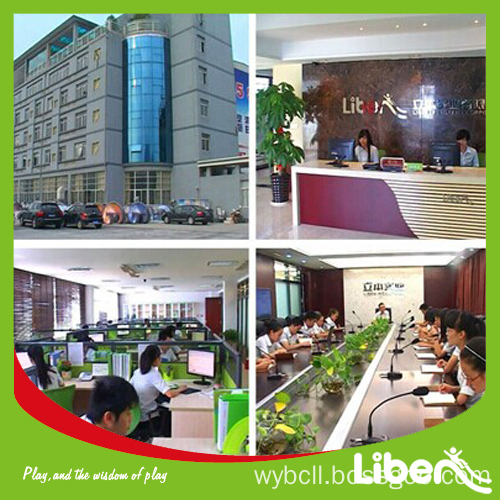
Candy Land Themed Indoor Playground Equipment
Candy Land Themed Indoor Playground Equipment, Plastic Indoor Playground, Soft Indoor Play
Liben Group Corporation , http://www.indoortrampoline.de